At every single level of your organization, there are tedious, repetitive, time-consuming, and manual tasks that your teams could do better or faster—and some that they don’t need to do at all.
If you could streamline or automate these tasks or eliminate them altogether, you’d make everyone’s job easier while accomplishing more with fewer people and less effort.
Pinpointing the problem areas is the first step:
- Which tasks take longer than they should?
- Which are the first to get back burner-ed when staff gets busy?
- Which are the most error-prone?
- What happens when tasks aren’t performed properly or don’t get done at all?
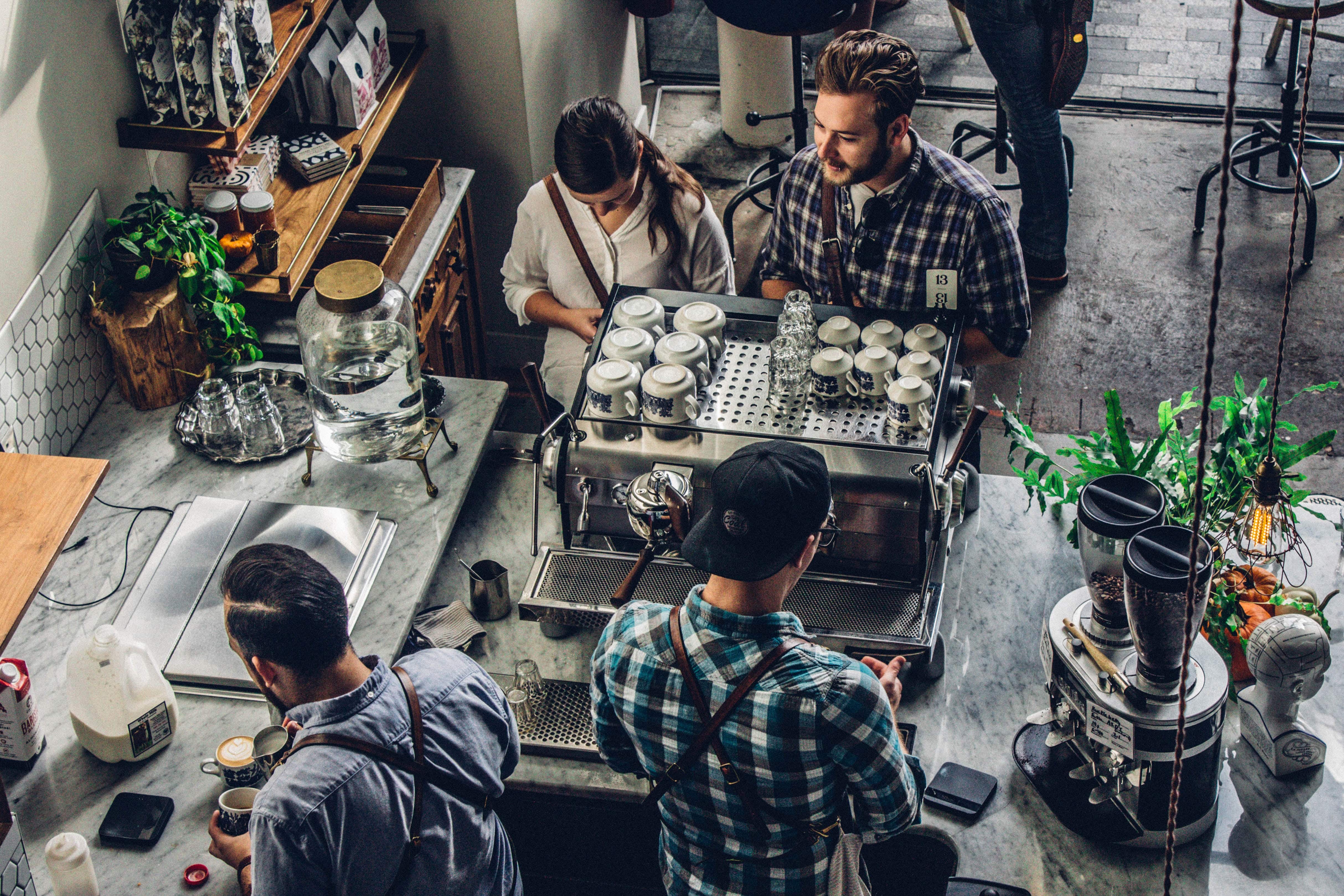
Once you identify those problem areas in your operation that are ripe for improvement, you can begin to explore which areas could benefit through the use of technology and automation.
Finding the Leaks in Store Team Productivity - How is Time Spent?
To find out the answers to these questions ourselves, we partnered with Technomic Inc. to conduct a research survey across the foodservice industry. Here’s what we discovered:
- Employees spend a lot of time on manual administrative work:
- 7.2 hours/week: average time spent by district/regional managers per week creating action plans for stores and following up on them
- 8-9 hours/day: average time spent by store employees per day to complete tasks throughout their shift
- 7.2 hours/week: average time spent by district/regional managers per week creating action plans for stores and following up on them
- Per the same study done by Technomic, multi-unit operators also find it difficult to hold each store accountable for completing important restaurant operating procedures like audits and corrective actions correctly and on time:
- 6.6 days: Average time it takes employees to complete corrective actions after a store audit
- Less than 50%: Amount of operators who are ‘very confident’ that action items are addressed properly coming out of an audit
- 6.6 days: Average time it takes employees to complete corrective actions after a store audit
As mentioned above, technology and automation can help operators address a lot of these challenges (plug those productivity leaks). As a technology provider, we wanted to better understand exactly how Zenput helps multi-unit operators and impacts their business. We recently surveyed our customers to gauge the return on investment that they see by using Zenput:
- At every level of a multi-unit operation, Zenput makes employees more efficient and more effective at doing their jobs. Here’s how:
- 5+ hours/week/per store: Time saved on manual, administrative work in each store with Zenput
- ~8 hours/week: Time saved by each district/regional manager
- 2+ more stores: Increase in amount of stores that each district/ regional manager is able to cover
- 10+hours/week: Amount of time saved per week on manual administrative work for HQ employees
- 5+ hours/week/per store: Time saved on manual, administrative work in each store with Zenput
- Operators using Zenput are also seeing improved quality at their stores and better execution. Here’s how:
- Zenput has improved external/3rd party audit scores by over 20% (Quality)
- Zenput has helped stores reduce compliance issues by over 24% (Quality)
- Zenput has improved external/3rd party audit scores by over 20% (Quality)
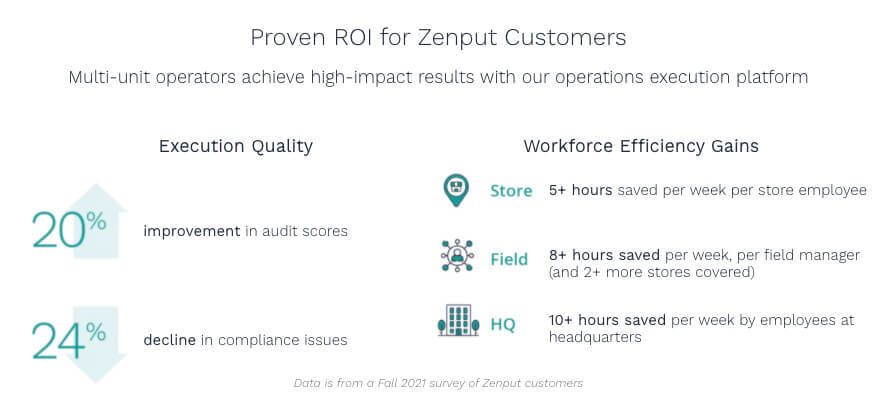
By giving valuable time back to HQ, field, and store employees and improving the execution of critical work being done in every location, operators that use Zenput are able to boost staff productivity with restaurant task management, and increase store performance across the operation.
To learn more about unlocking employee productivity and how Zenput’s OpsX platform can help you unlock efficiencies across each level of your operation, download The Operator’s Guide to Productivity in a Short Staffed World.
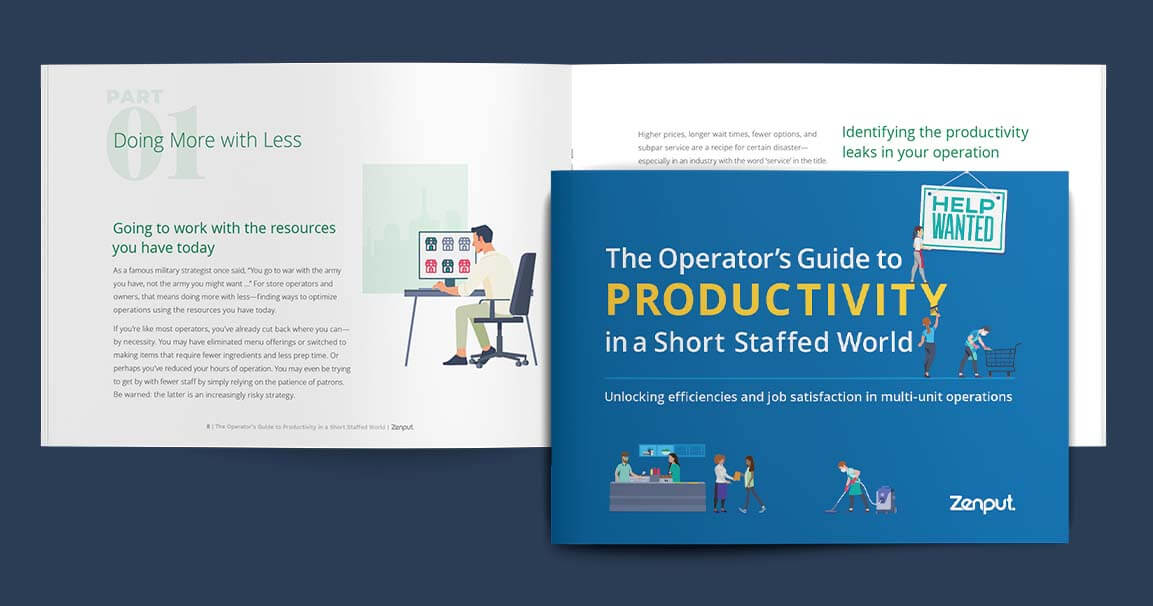
Subscribe to our blog
You are now subscribed!