Short-staffed or not, the show must go on. Multi-unit operators still need to cook, clean, sanitize, prep, check, label, etc., every day in every store, and maintain quality standards every step of the way. With fewer workers available to complete everything that must be done on a given day, the result is heavier workloads for the crews that do show up. Something’s got to give—and it can’t be quality, safety, service, or cleanliness.
Multi-unit operators are using technology to ease the pressure on this worker shortage in two major ways:
- Increase employee productivity
- Attract and retain workers by giving them tools that will help them do their job better, and make it more enjoyable
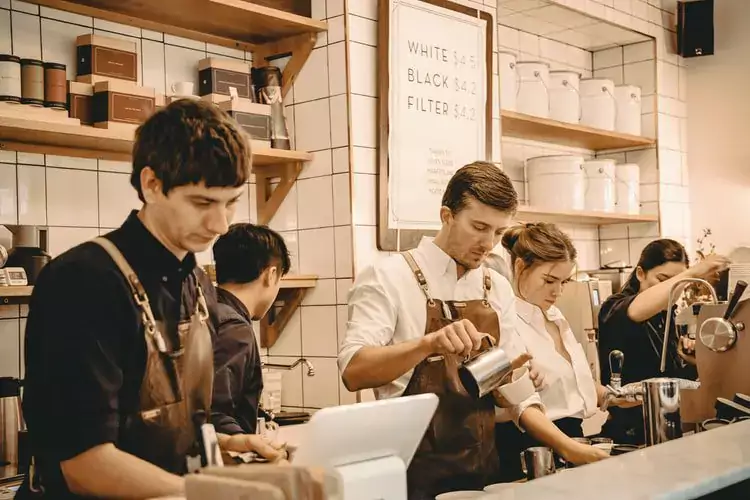
A robust OpsX platform can help drive the productivity of employees in the field and in your stores, and improve the consistency of work happening throughout your entire organization.
Here’s how:
1. Automate manual work in the store → Stay ahead of food safety risks by reducing manual work for store employees and ensure that tasks are performed correctly and on time, allowing them to focus on higher-value work, like interacting with customers.
Why?
- Food prep labeling is a critical aspect of food safety, but when done manually, it can eat up a ton of valuable staff time and risk costly downstream mistakes (e.g., mislabeled products, incorrect expiration dates).
- Reduces margin of error
- Eliminates another mundane task
- Ensures food prep is done correctly and on time
- Food temperature monitoring is another key area where automation saves staff time, reduces food safety risks, and increases productivity. Manually checking equipment temperatures, such as coolers, freezers, and makelines, every couple of hours is tedious and time-consuming.
- Automatically generates alerts when temps go out of range
- Immediately assigns follow-up tasks to managers
- Gets store staff out of the freezer and back in front of customers
How: Zenput makes it easy to automate the process of triggering the right corrective actions when issues are flagged – and monitoring them through resolution. This means shift workers don’t have to spend a lot of time calling, emailing, texting to get flagged audit issues resolved.
- Food Prep Labeling: Operators use Zenput to automate critical steps in the food labeling process, including product identification, calculation of expiration dates, and more.
- Store employees simply select from a predefined list of products and ingredients available on a mobile app to quickly and easily print food prep labels. Zenput automatically calculates expiration dates based on the product selection and the current date and time.
- Automated food labeling shaves as much as 30 minutes off food prep time and reduces the likelihood of preparing and serving past-date products to customers.
- Store employees simply select from a predefined list of products and ingredients available on a mobile app to quickly and easily print food prep labels. Zenput automatically calculates expiration dates based on the product selection and the current date and time.
- Temperature Monitoring: Zenput’s temperature monitoring system automates temperature monitoring.
- Sensors automatically generate mobile alerts when temperatures go out of range, notifying the right personnel to identify and address issues as quickly as possible. This frees up store staff to handle more meaningful tasks, like serving customers.
- Zenput customers use this approach to reclaim 60 minutes/day (or more) of labor time in every store location.
- Sensors automatically generate mobile alerts when temperatures go out of range, notifying the right personnel to identify and address issues as quickly as possible. This frees up store staff to handle more meaningful tasks, like serving customers.
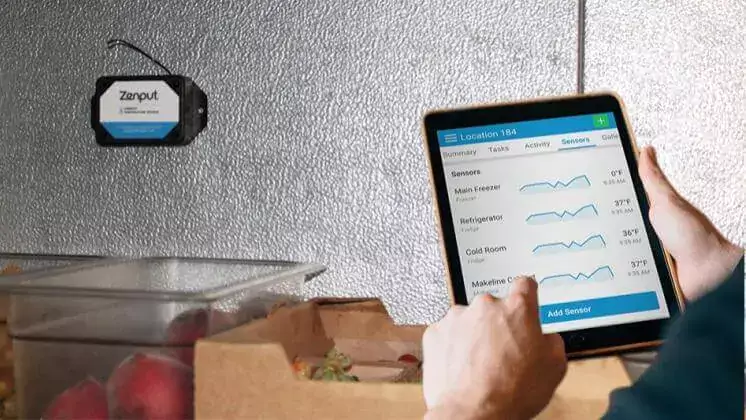
2. Focus district manager time and attention with remote visibility in the field → Field managers can’t physically be everywhere at once, and as a result, can lack visibility into where the biggest issues are surfacing, which makes it difficult to prioritize time and attention accordingly.
Why? With remote visibility, field teams can oversee store performance and perform audits more efficiently even when they’re not on-site, giving them time back to spend on employee coaching and training.
- Give field teams eyes in every store
- Help identify short-staffed locations that are struggling
- Empower field managers to quickly funnel resources where they’re needed most
How: Zenput provides a virtual window into operations at every location—right from their mobile device or computer. Even when not onsite, field teams have instant visibility into the operation, so they can funnel resources and attention to the locations that need it most.
- Zenput Best Practice: For completion percentages in Zenput, they can plan their daily visits according to the completion gaps. As you can imagine, the stores that are executing daily standards at a lower rate also tend to be lower staffed or higher volume and benefit the most from a field leader's support on any given day.
3. Digitize procedures at corporate headquarters → If your organization is still shuffling papers back and forth between store locations, field leaders, and HQ, you’re wasting valuable time. If you need to share important news or make a simple update to a standard operating procedure, it shouldn’t take weeks or months to get it done. The digital era has arrived, and the sooner you embrace it, the better for more efficient operations.
Why? More agility allows operations teams to quickly automate the rollout of new initiatives or updates to procedures and gives them visibility into potential issues before they impact the business.
- Instantly update teams and assign tasks
- Eliminate costly paper-based processes
- Take tedious, error-prone administrative tasks off everyone’s plate
How: Zenput’s fully customizable form builder lets you create and edit digital forms, checklists, audits, and more, and instantly make the most recent versions accessible to your teams no matter where they are. Building out all your standard operating procedures in Zenput means that everyone in the organization, from HQ down to the stores, always knows the status of the work being done. That means no more copying, scanning, printing, mailing, shipping, or faxing.
To learn more about unlocking employee productivity and how Zenput’s OpsX platform can help you unlock efficiencies across each level of your operation, download The Operator’s Guide to Productivity in a Short Staffed World.
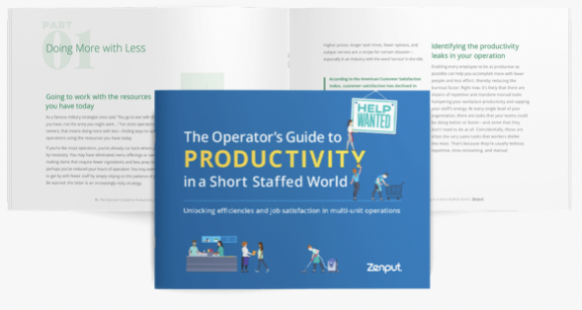
Subscribe to our blog
You are now subscribed!